NUTEC Bickley's box furnaces are ideal for intermittent or batch processes where the product is front loaded directly into the furnace with the help of a forklift/handling gear.
Technology Offered
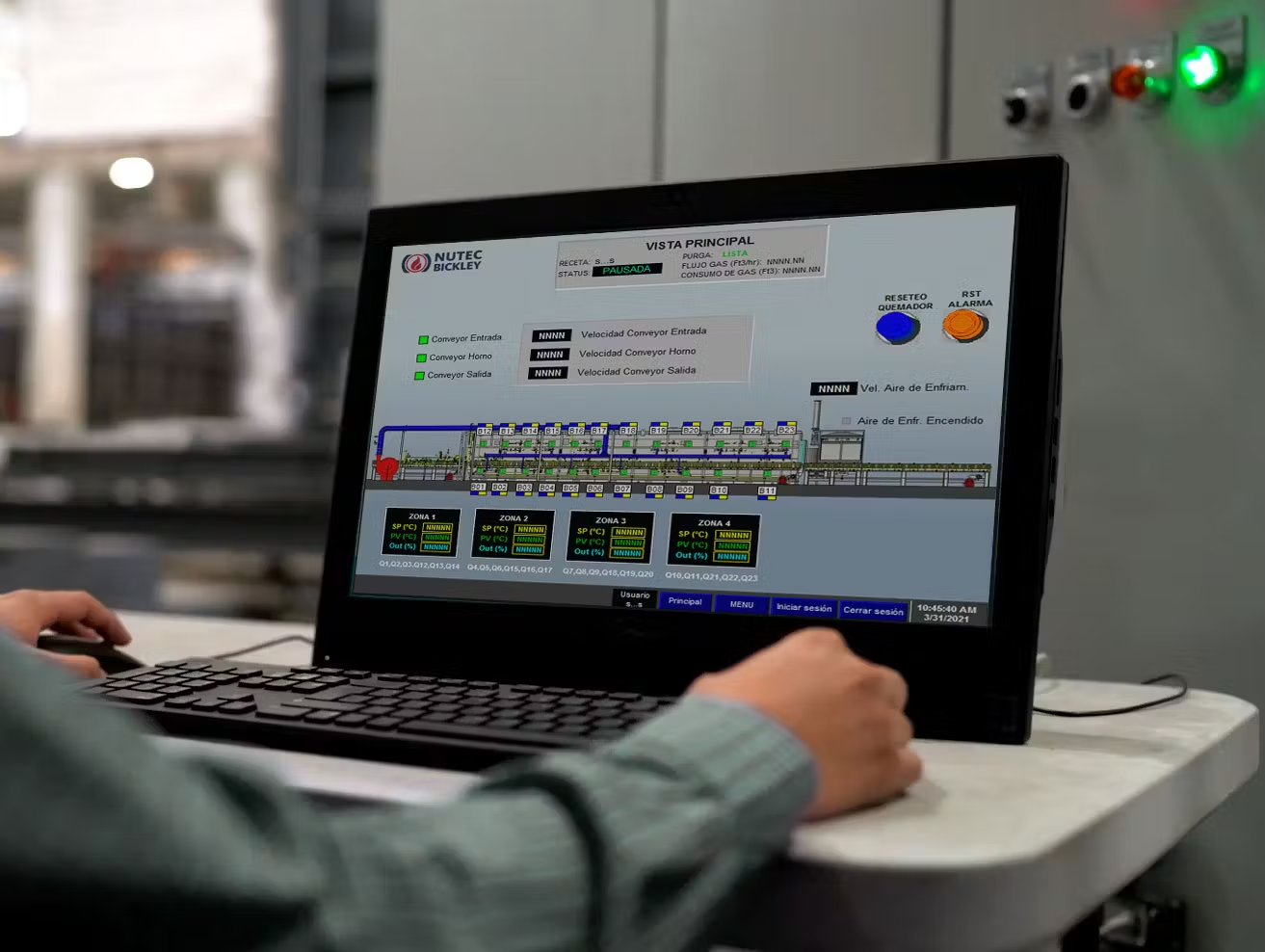
SCADA
With our SCADA systems, kilns operators are able to have complete control of their firing process, enhancing efficiency and productivity.
Learn more about SCADA