The flexibility of the car bottom furnaces makes it a popular choice for processes that require batch handling, large and unusually shaped parts, or multiple configuration loads.The car bottom furnaces design offers the great advantage of having the capacity to handle large/heavy product loads, as the product is loaded on the floor of the cart(s) when it’s outside the oven area, eliminating damage to the furnace interiors during loading and unloading.
These car bottom furnaces can be designed to operate at low temperatures in tempering processes, annealing at higher temperatures, and even reheating forging
at even higher temperatures.
With these furnaces, one of the key features is the ability to seal the perimeter of the car to the inner chamber. Our designs include fiber lift seals, which are actuated by pneumatic cylinders and mechanical means to provide an effective seal that minimizes cold air infiltration and heat losses, which could otherwise cause wear and thermal damage to the substructure.
Another critical area is the perimeter door seal, which can be achieved through a variety of methods using refractory materials that allow for compression and sealing while also providing a solid, damage-resistant surface that will last over time.
Technology Offered
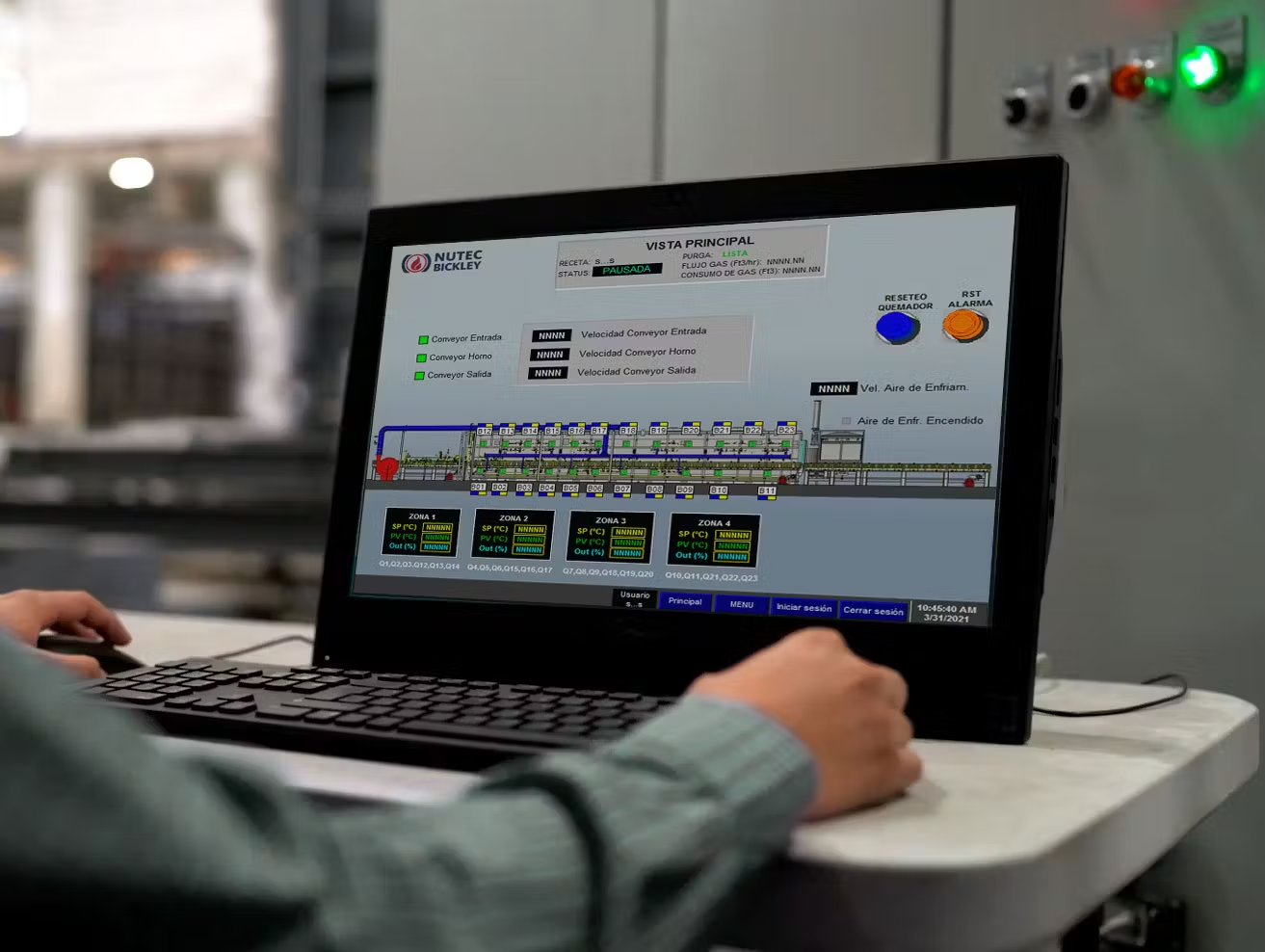
SCADA
With our SCADA systems, kilns operators are able to have complete control of their firing process, enhancing efficiency and productivity.
Learn more about SCADA